Summary
The rise and fall of a business depends to a great extent on how it manages its suppliers. The massive disruptions to global supply chains caused by the Covid-19 pandemic underscored the importance of resilient procurement systems in business. Despite the challenges, organisations with strong procurement processes managed to keep costs and risks low, collaborate smoothly with existing suppliers, identify new supply sources, and stay profitable.
Given its importance, this article takes a deep dive into the meaning of procurement, the steps involved in the procurement process, the types of procurement, and what it takes to develop a robust and agile procurement system for your business.
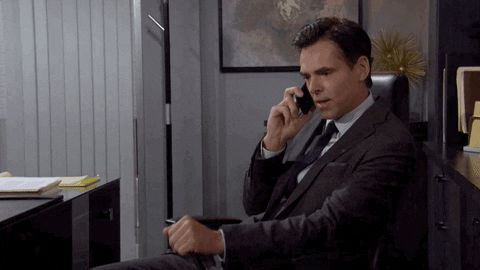
What is procurement?
Whether you run a clothing store, provide IT solutions, or assemble and sell electronic products, you cannot do without procurement. But the definition of procurement is a lot broader than it seems. This procurement definition by global management consultant Gartner sums it up nicely: Procurement is a corporate function that governs a company’s purchasing decisions. Activities of the procurement function include strategic vendor evaluation and selection, competitive bidding, contract negotiation, and purchasing. Effective procurement practices enable organisations to reduce costs and maximise value
Steps in the procurement process
There are three broad stages in the procurement process – sourcing, purchasing, and payment. These can be split further into nine steps:
- Identify the goods (or services) your business needs. It could be new goods you haven’t bought before or previously bought goods you need to stock up on.
- Submit a purchase requisition to the procurement team detailing the goods required, their quantity and price, the time you need them by, and so on. The procurement team will review the request and approve it if everything is in order.
- Assess and select a supplier.
- Negotiate the price and other contract terms.
- Send a purchase order to the supplier.
- Receive the goods and inspect them.
- Prepare an invoice after confirming that the goods match the purchase order.
- Approve the invoice and make the payment.
- Record the procurement process in its entirety for future reference.
As is evident from the nine steps, procurement is defined by the three Ps:
- People: The stakeholders with distinct responsibilities at different stages of the procurement process. Effective procurement management happens when businesses assign the right person to each step or task.
- Process: Procurement is a continuous, ongoing process rather than a series of one-off actions. This is why the term procurement life cycle is often used to describe the procurement process. Each step must move in tandem with the next for a smooth procurement experience that is devoid of errors, delays, and quality issues.
- Paperwork: From purchase requisitions and purchase orders to vendor contracts and invoices, documentation is key to procurement. Record-keeping is an essential part of the process.
Procurement, purchasing, sourcing, and supply chain – know the difference
These terms are often used interchangeably, but there are distinct differences.
Purchasing versus procurement
Purchasing is one component of procurement. Purchasing is the act of buying goods and is, hence, transactional in nature. Procurement has a broader context. It involves not just buying the goods but exploring multiple buying options, selecting the best option based on certain criteria (cost, time, supplier location, etc), and developing long-lasting relationships with suppliers. Purchasing is reactive, fulfils a short-term goal, and is almost always focused on price. Procurement, on the other hand, is proactive, and works towards long-term goals such as building brand value and gaining competitive edge. Furthermore, it places importance on the value of the goods rather than simply on their price.
Sourcing versus procurement
Like purchasing, sourcing is a component of procurement. It comes before the purchasing stage. Sourcing involves finding the best supplier for your goods. Sourcing activities include identifying and assessing potential suppliers, negotiating terms with them, and selecting the best among them.
Supply chain versus procurement
Supply chain activities include turning raw material into finished goods, managing the various stakeholders along the supply chain (suppliers, manufacturers, distributors, retailers, and buyers), and handling the transport and logistics (freight ships and planes, warehouses, containers, etc) used to deliver the goods to the final customer. What sets it apart from procurement is that it comes in the post-contractual phase whereas procurement is largely pre-contractual (supplier selection, negotiating, buying, etc.).
Principles of procurement
Most publicly owned businesses follow an ethical code of rules when they undertake procurement activities because these are funded by taxpayers’ money. Many private businesses have also adopted these rules or principles of procurement, the most prominent of which are:
Value for money
This means selecting the offer with the best possible price – not necessarily the lowest – without compromising on quality. It takes into account the total cost of procuring the goods concerned (from planning to disposal) and the risks involved. It ensures that the goods are obtained and the needs of the business are met in the most efficient way.
Competition that guarantees fairness, transparency, and integrity
An organisation with an ethical procurement management style invites bids from multiple suppliers and chooses the best. It ensures that the competition is fair to all the suppliers and not preferential to some. It must also be transparent, with the competitive processes open to all eligible suppliers. Finally, the competition must ensure honesty and integrity by using the funds for their earmarked purpose and nothing else.
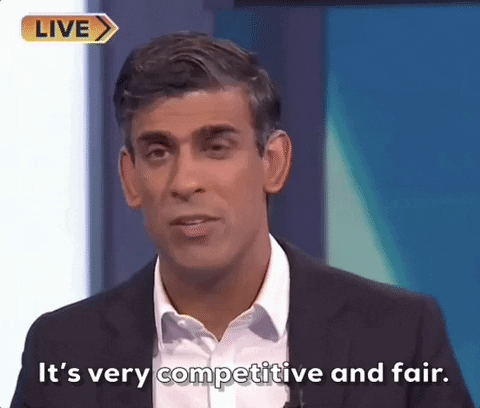
Efficiency
This means getting maximum value from a procurement activity while reducing transaction costs and avoiding delays.
Accountability
The people involved in the procurement process must understand their responsibilities and be held accountable for their actions. This will reduce ambiguous decisions, delays, and errors.
Objectives of procurement
You might have heard about the five rights of procurement – getting the right quality, in the right quantity, at the right time, for the right price, from the right source. This is the primary reason why a business needs an effective procurement process. In order to deliver on these five rights, the procurement process must work towards achieving the following objectives:
Supply assurance
First and foremost, procurement managers must ensure a steady, uninterrupted supply of goods for the company whenever the need arises.
Building a robust supplier base
Most businesses are dependent on suppliers. A procurement process exists to help companies build a robust and reliable supplier base that caters to all its needs, even on short notice. The road to developing the ideal supplier network starts with careful assessment and selection of vendors based on well-defined rules and standards. It requires periodic evaluations to monitor how they meet requirements and expectations. Finally, taking the trouble to build lasting relationships with suppliers ensures that they offer you their best services at all times.
Operational efficiency
The process of procuring goods and services involves multiple departments. If the sales team unilaterally enters into contracts with suppliers and other departments similarly work in silos, there’s bound to be confusion. Businesses set up procurement systems with the objective of managing these multiple internal operations efficiently and making them cohesive. Some of the ways in which procurement managers optimise internal operations are by hiring and training staff for specific procurement activities, defining policy, identifying and mitigating risks, implementing efficient and transparent invoicing and payment systems, and so on.
Risk management
Procurement managers are well-informed about the latest market trends, pricing changes, material shortages, and other important events. They have the ability to analyse and interpret how these events might impact the organisation. Involving the procurement team in all aspects of business is critical to ensuring the organisation is not caught off-guard by a sudden disruption or has a solid contingency plan in place when it faces an unavoidable crisis. The knowledge and insights a business gains from its procurement team can elevate its decision-making, strategy formation, and risk management capabilities.
Types of procurement
Procurement can be categorised in the following ways:
Direct procurement
This refers to the purchase of an item that is used to manufacture a finished product – for example, raw material, parts, or equipment. Buying wholesale goods for resale is also an example of direct procurement.
Indirect procurement
This covers purchases that aren’t involved in the manufacturing process but are essential for a business’ day-to-day operations. Buying office supplies and furniture or hiring a consultant are some examples of indirect procurement.
Goods procurement
As the name suggests, it refers to buying physical items and includes both direct and indirect procurement. Typical examples include raw material, components, office furniture, and even software subscriptions.
Services procurement
This covers the procurement of people-based services such as hiring consultants, lawyers, contractors, maintenance personnel, and security personnel.
Traditional procurement versus strategic procurement
The events of the past two years have shown how vulnerable global supply chains are to sudden disruptions such as soaring freight costs, container shortages, and a scarcity of raw materials. Given that these challenges aren’t a one-off, businesses must upgrade their traditional procurement processes that focus primarily on the price of goods. Traditional procurement must give way to strategic procurement, which measures the total cost of procurement, from transactional and administrative costs to transportation, delivery, and inventory cost.
What sets strategic procurement apart from its traditional counterpart is that it relies heavily on data collection and analysis. Businesses with a strategic procurement process use data to understand the types of goods and services they require. They conduct market research to find the best suppliers. They also study their spending patterns to make sure their procurement processes are cost-effective but don’t compromise on quality.
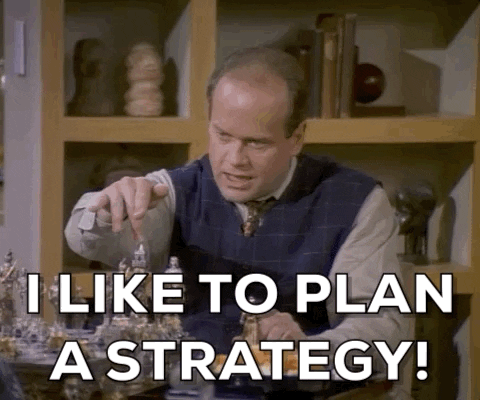
To gain a deeper understanding of strategic procurement, let’s take a look at its five pillars:
1. Procurement strategy
Strategic procurement needs a long-term plan that makes it possible to buy goods at the best price, quality, and time and on the best terms. An effective procurement strategy should clearly define procurement objectives and policies, supplier requirements, selection processes, and more.
2. Category management
This is a procurement tactic that bundles similar goods required across the organisation. The bundling ensures that the goods are bought under a single contract and for one price. As a large contract attracts a lower per-unit price as well as volume discounts, category management maximises savings and optimises spend management.
3. Strategic sourcing
This is a process where businesses analyse spending patterns to select the best suppliers who offer them the highest value in the market.
4. Contract management
Strategic procurement requires effective contract management, which covers the creation and execution of agreements to their analysis and review and everything in between. Contract management is key to keeping costs low while ensuring a high level of performance from suppliers.
5. Supplier management
As mentioned earlier, supplier management is the art of fostering deep, long-lasting, and mutually beneficial relationships between a business and its suppliers.
Traditional procurement versus strategic procurement
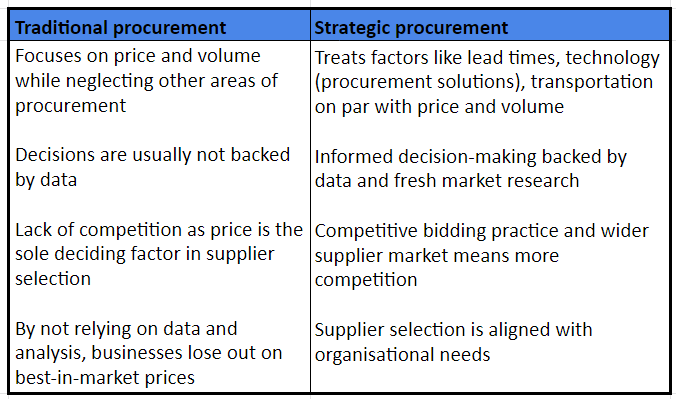
Procurement models
When it comes to implementation, businesses can choose between five operating models for their procurement needs. Here, we’ll see what each model entails and the pros and cons of each, based on which you can decide what model works best for your business.
Local
Also called decentralised procurement, each department makes its own decisions, carries out its own procurement activities, and works autonomously with little to no oversight. The advantages of local procurement include direct contact and close ties with suppliers, fast purchasing, and a high level of responsiveness. The downside is a lack of coordination between departments and compliance issues, leading to an unstructured and often messy procurement system. A common fallout is an organisation drawing up two separate contracts and paying two different suppliers different prices for the same product. There is, therefore, a definite risk of losing out on more cost-effective buying options.
Network
Procurement-related decisions are not taken independently but managed by one or more authorities. The result is coordinated procurement activity between departments and greater compliance. There is also more room for cost savings. However, some of the advantages of a decentralised system might be lost.
Central
Both decision-making and procurement activity are controlled by a single procurement department. A centralised approach leads to standardisation, higher compliance, and better risk management, which increases overall operational efficiency. Discounts offered by suppliers on large purchase volumes and the absence of maverick spending increases cost savings. However, purchasing time might be longer than in a decentralised system.
Federal
This is a combination of the local and central models. Through this hybrid approach, some items are procured locally and others centrally. While teams enjoy a certain degree of autonomy performing procurement tasks at the local level, it is not at the same level of complete autonomy one would see in a fully local procurement system. In a federal system, the level of autonomy is determined by mutual agreement or dictated by the central authority, resulting in a higher level of compliance.
Central network
Another combination model, this one is a fusion of central and network procurement. There is coordination between departments and one or more points of authority, with the primary authority lying with the centre.
Importance of data in procurement
Information is power. Here are the ways in which data collection and analysis is aiding procurement:
Informed decision-making
By collecting and analysing correct and consistent procurement data, businesses can greatly improve decision-making. Armed with valuable insights drawn from data and knowledge of the latest market trends, they are better positioned to take advantage of opportunities when they arise and take precautions when conditions are risky. Data-backed decisions have a greater chance of success than decisions based on intuition. They also help to make businesses more agile, proactive, and profitable.
Cost savings
According to a McKinsey study, data and analytics in procurement improves cost savings by 3% to 8%. Studying historical data and spend patterns allows you to compare the prices at which you previously bought similar products. You can also compare your suppliers and the prices they offer. This information can be used to negotiate better rates and contract terms. Procurement data is also useful in planning procurement strategy in such a manner that it not only gives you the best price options but also the maximum value.
Happy, hard-working suppliers
While it is good to build relationships with suppliers, it is important to evaluate them on the basis of facts (data) and not emotions. A company’s historical data holds valuable information about its suppliers’ performance – for example, how consistent they have been in delivering the required goods, and how they compare with each other in terms of pricing. Furthermore, having a repository of supplier data vastly improves a company’s dealings with its suppliers, reducing the likelihood of delays and misunderstandings.
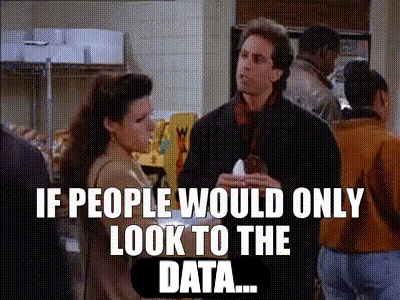
Procurement KPIs
How effective is your procurement process? By using key performance indicators (KPIs) related to cost, quality, time, and other important factors, you’ll have a fairly good idea of whether your procurement process is a success or failure. Here are five common KPIs:
Supplier defect rate
This is the ratio of the number of low-quality products to the total number of products tested. A high defect rate puts a question mark on the supplier’s reliability and leads to unwanted expenses.
Lead time
Lead time is the time taken to deliver the goods after the order is received. While it is reasonable to allow your suppliers a certain degree of flexibility in producing and shipping your goods, the average lead time should remain consistent. Long lead times affect profit and cause losses.
Emergency purchase rate
Unplanned purchases to prevent inventory shortages are unavoidable, but become harmful if done too often. Monitoring and checking the rate of emergency buys is essential to save money, lower risk, and ensure supply continuity.
Vendor availability
As we said in the point above, emergency buying to meet increased demand is unavoidable at times. Therefore, it’s always good to know if your suppliers are capable of producing and delivering goods on short notice and if they can do it reliably.
Compliance rate
Your suppliers’ failure to comply with contract terms and safety and quality standards could lead to legal trouble for your business. To measure compliance rate, check the ratio of disputed invoices to total invoices or the differences between quoted price and the final price paid.
Procurement solutions
Procurement solutions are growing in popularity in the digital age. By digitising activities such as invoicing, purchasing, and spend management among others, these solutions streamline and optimise procurement processes so that they are resilient even in difficult conditions. Procurement solutions benefit organisation in the following ways:
- They automate repetitive manual tasks such as data entry, increasing their efficiency and reducing the likelihood of human error. They also allow you to store all your data in a centralised database and control access to it and secure it with admin settings.
- Procurement solutions automate and optimise approval processes, lowering the risk of delays and bottlenecks, which can cause considerable financial harm. With even modestly sized businesses dealing with multiple purchase orders, invoices, and purchase requisitions in a day, automated approvals are definitely advantageous.
- They create standardised procurement policies and processes, which ensures transparency and consistency in operations and in the way a business treats its suppliers.
- With automated payment solutions, chances of missing payments are low. Plus, you have complete visibility over your spend in real time. Timely payments are crucial to maintaining good ties with suppliers. What’s more, most payment solutions easily integrate with your company’s accounting software.
- They make tasks like getting feedback from stakeholders and monitoring KPIs easier. By using this data, you can make continuous improvements to your procurement process.
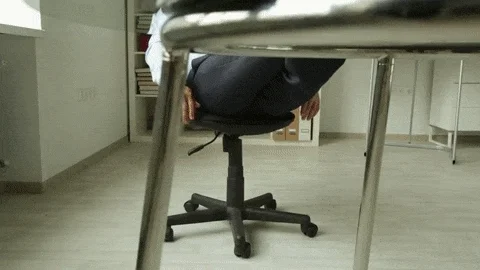
How to choose the right procurement solution for your business
Here are some factors to consider before settling on a procurement solution:
- It must be easy to implement. There is always resistance when changes are introduced in the way we work. With procurement solutions, there are technical challenges to overcome as well. That is why the chosen solution must be one that your employees can adapt to easily and get running in a short period of time.
- Check the features carefully. An easy-to-use interface, automatic initiation and approval of purchase orders and purchase requisitions, three-way matching of invoices against relevant purchase orders and received goods, and features that improve communication such as in-app alerts and automatic notifications are good-to-have features. On the flipside, there might be features you don’t need and shouldn’t pay for. So, consider alternative solutions and pick the one that fits your needs and budget. Most procurement solution providers also offer customisation, which is an option worth having.
- Customer support is non-negotiable. Glitches and snags are common when businesses switch to a new technology or software. Make sure the service provider offers prompt support. Before signing a contract with them, ask them how long they take on average to respond to and resolve problems once a ticket is raised. If they are not forthcoming with the information, you might want to look elsewhere.
- The procurement solution should complement your accounting software and integrate seamlessly with it to ensure accuracy and efficiency.
5 procurement best practices
- Automate manual processes to save time, improve accuracy and efficiency, and reduce human error. Automation and digitisation are the first step to making your business competitive. They also allow your employees to focus on more important matters.
- Create a centralised procurement database for the whole company so that all decisions are based on common data. Multiple clusters of data give rise to inconsistency and errors. Also, make sure the information in the database follows a common language and methodology.
- Make sure communication is smooth and seamless through the supply chain. When a company’s departments (finance, procurement, planning, etc), suppliers, and supply chain partners are united by a continuous flow of information, there is better collaboration between them.
- Advocate transparency. Making compliance and due diligence part of procurement culture will ensure you don’t get stuck with unfavourable contracts and don’t have to come up with hasty solutions each time a problem crops up. Companies that prioritise transparency and accountability are also more attractive to business partners and enjoy an exalted reputation.
- Be analytical. Use the vast amounts of data at your disposal to power your decisions, explore opportunities, mitigate risks, and make forward-looking, long-term plans that will help your business grow.
How Aspire can help your procurement process
Take your procurement process to the next level with these Aspire products:
- Bill Pay is an AI assistant that can help you automate your invoices, so you never miss a payment deadline. A single email is all it takes to get set.
- Expense Management offers in-app expense and claim approvals, and real-time visibility on your company spend.
- Payables Management comes with integrated accounting and invoicing as well as all your revenue and expenses on a single dashboard for complete visibility.
- Budgets allows you to create budgets at project or team levels and to split your company spend into categories to maintain total visibility.
- All these products are easy to use and sync with your accounting software.